The Reflection
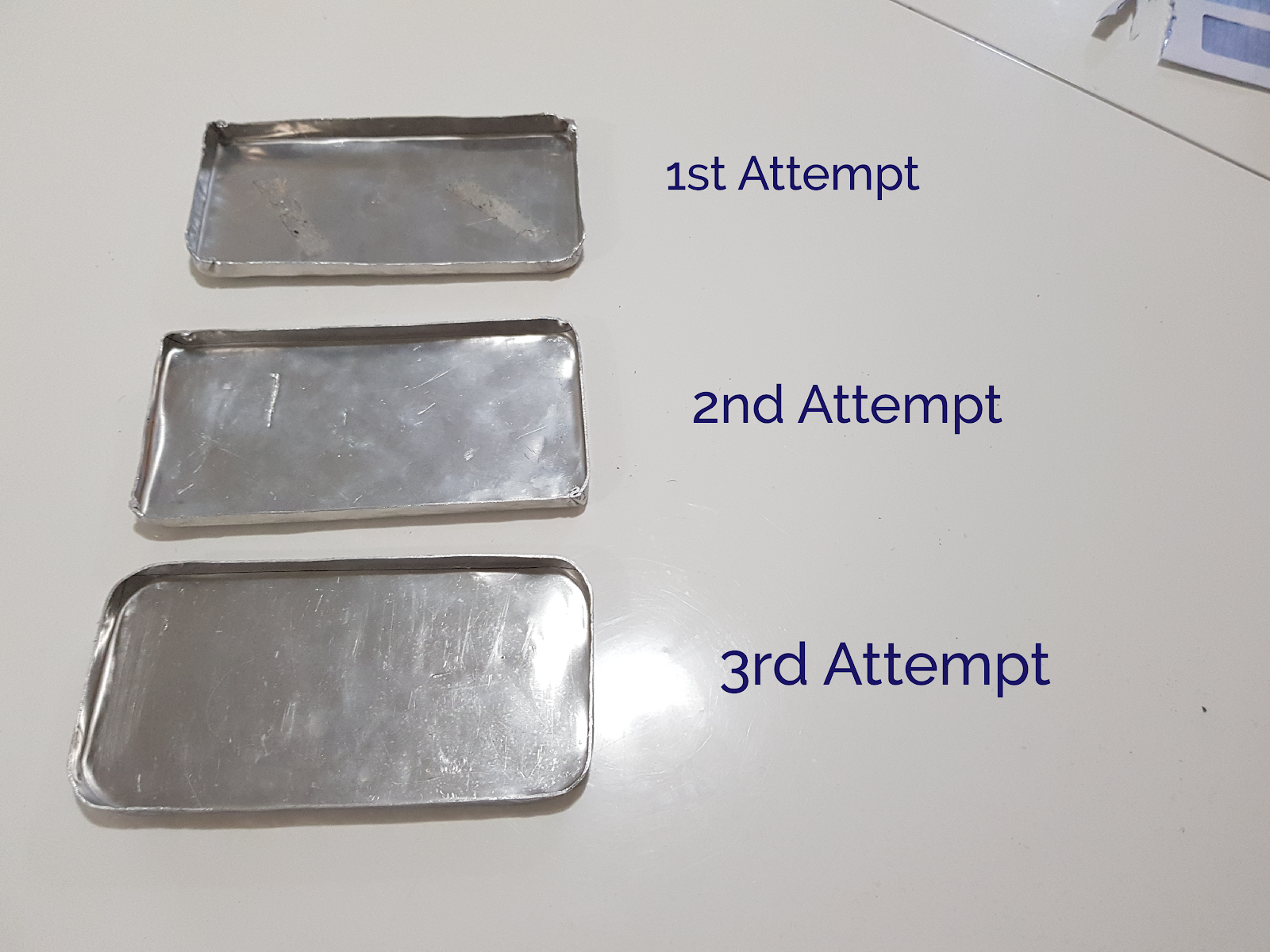
As an Industrial Design student, model making is model making is no stranger to me, however, I've only touched metal once throughout my studies and it was just a simple cutting and bending of a 0.5 mm aluminium. The rest of the times, we usually made models from blue foams, 3D printing, and wood works, which is why metal working in this class felt like a whole new world. Throughout this class, I have learned new things and skills on metal shaping, which will be helpful in future model making especially where metal is involved and metal is quite common in product design. For this critical review task, I chose to review the tray, as it is the one i found most difficult, and took me the most tries to nail it. The Tray The tray was the most difficult task for me, even more than the tank in my opinion. There's so much room for errors with the tray compared to the tank. The tray took a total of 3 tries before i got a decent one. 1st Attempt From a